What Is Rim Injection Molding?
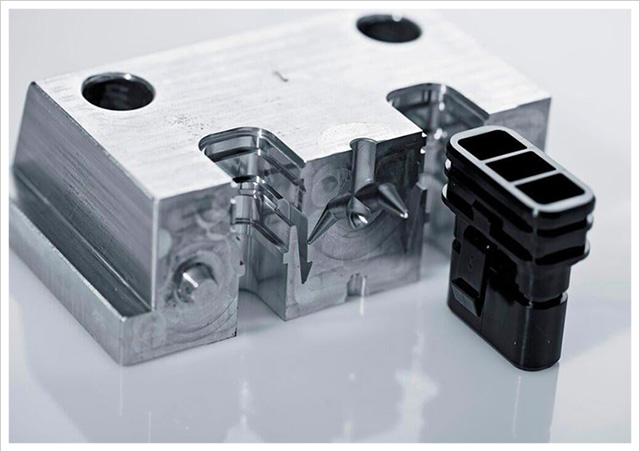
Accel Precision Machine and Mold offers Reaction Injection Molding (RIM) as part of our comprehensive machine shop services. RIM is a unique process that creates strong, lightweight, and complex parts with high precision and accuracy.
Our RIM service is perfect for various applications, from automotive and aerospace to medical and consumer products. By utilizing RIM technology, we can produce parts with a wide range of shapes, sizes, and textures that are both durable and cost-effective.
RIM Mold Experts
Our team of experts is highly trained in the latest RIM techniques and is dedicated to providing the highest quality products and services to our customers in Denver, CO. We work closely with our clients to understand their specific needs and requirements and provide customized solutions that meet their unique needs.
At Accel Precision Machine and Mold, we are committed to staying at the forefront of innovation and technology in the machine shop industry. Our RIM service is just one of the many ways we are making a difference in the manufacturing world. Contact us today to learn more about our RIM capabilities and how we can help you with your next project.
Advantages of Reaction Injection Molding
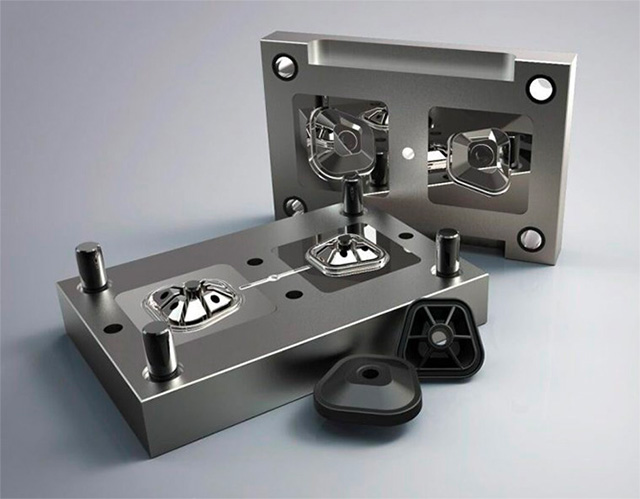
The reaction injection molding process has several advantages over other plastic molding processes, including:
Design Flexibility: Reaction injection molding allows for complex designs and shapes to be molded in one piece without requiring assembly. This is due to the low viscosity of the liquid mixture, which allows it to flow easily into tight spaces and fill intricate mold cavities.
High Strength and Durability: The resulting polyurethane parts are strong and durable, with excellent mechanical properties. The parts are resistant to impact, abrasion, and chemicals, making them ideal for a wide range of applications.
Low Cost: Reaction injection molding is a cost-effective way to produce small to medium-sized runs of plastic parts. The low-pressure process means molds can be made from cheaper materials, and the short cycle times reduce labor costs.
Fast Cycle Times: The reaction injection molding process is fast, with cycle times typically ranging from a few minutes to a few hours, depending on the part size and complexity.
Disadvantages of Reaction Injection Molding
Despite its advantages, the reaction injection molding process has some disadvantages, including:
Limited Materials: The RIM process is limited to polyurethane and some other reactive polymers. This means that it may not be suitable for all applications.
Mold Design: The mold design for RIM is more complex and expensive than for other plastic molding processes due to the need for special features such as venting and gating.
Environmental Concerns: The reaction injection molding process requires isocyanates, which are toxic and can pose health and environmental risks if not handled properly.
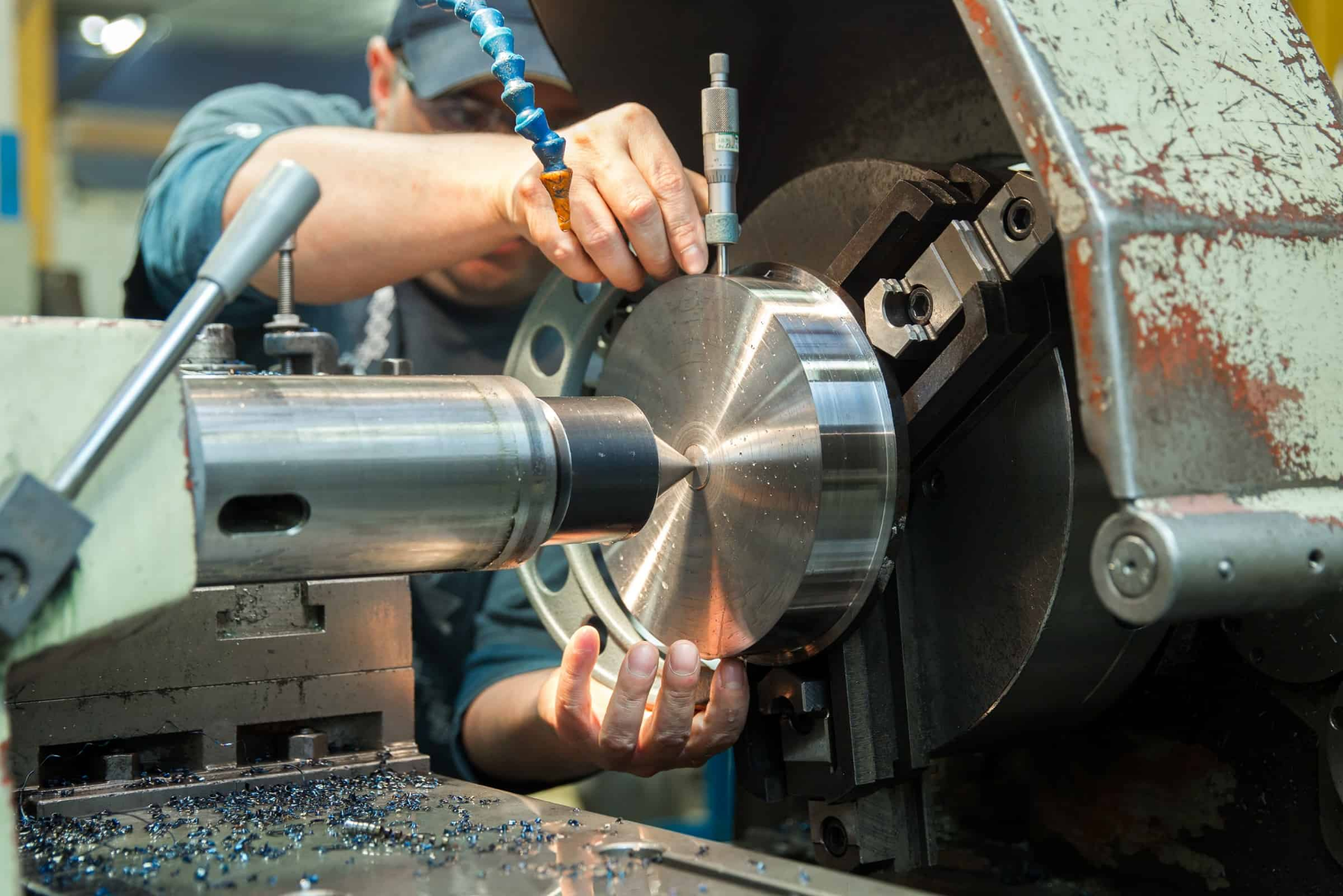
Our Mold and Machining Services
The reaction injection molding process is used in a wide range of industries and applications, including:
Automotive: RIM can produce high-quality plastic parts for car interiors and exteriors, including bumpers, spoilers, dashboards, and seats.
Medical: RIM is used to produce medical equipment and devices, such as surgical tools, orthopedic devices, and prosthetics.
Consumer Goods: RIM produces various consumer goods, including toys, household appliances, and electronics.
Aerospace: RIM produces lightweight, high-strength parts for aircraft and spacecraft.
Industrial: RIM produces parts for industrial equipment, such as pumps, valves, and conveyor systems.
Available Materials for Reaction Injection Molding
The reaction injection molding process is typically used to produce parts from polyurethane and other reactive polymers, including:
- Polyurethane: This is the most common material used in RIM, due to its excellent mechanical properties, low cost, and ease of processing.
- Polyurea: This is a more flexible material than polyurethane, with excellent
- abrasion and chemical resistance.
- Epoxy: This material is known for its high strength and excellent adhesion properties. It is commonly used for parts that require a high degree of stiffness and dimensional stability.
- Silicone: This material is used for parts that require high temperature resistance, such as seals, gaskets, and electrical insulators.
Summary
Reaction injection molding is a versatile and cost-effective way to produce high-quality plastic parts with complex designs. The process offers several advantages, including design flexibility, high strength and durability, low cost, and fast cycle times. However, its disadvantages include limited material options, complex mold design, and environmental concerns.
Get a Free Consultation for Reaction Injection Molding
If you are considering using the reaction injection molding process for your manufacturing needs, contact Accel Precision Machine and Mold for a free consultion.
We can help you determine whether RIM is the right process for your project, assist with mold design, and provide guidance on material selection.